Biomicrogels® chemicals demonstrated high efficiency and cost-effectiveness for metalworking fluid separation at PJSC Severstal
In September 2020, the experts from SPC BioMicroGel have completed a series of successful pilot tests for separation of spent cutting fluids (coolant lubricants) at the plant of PJSC Severstal in Cherepovets. The coagulating agent BMG-P2-02-03 used in these tests has proven its effectiveness, having purified the water up to the levels specified by the customer.
Over time, metalworking fluids that are widely used in manufacturing processes are becoming inefficient and need to be disposed of. The emulsion of cutting fluids is stable and almost does not decompose by itself, therefore such emulsion can’t be discharged into water bodies or water treatment facilities without preliminary deactivation and purification. The evaporators used for these tasks have massive energy consumption, the filtering equipment quickly clogs up and requires frequent replacement of filter elements, and standard reagents do not provide the required cleaning efficiency.
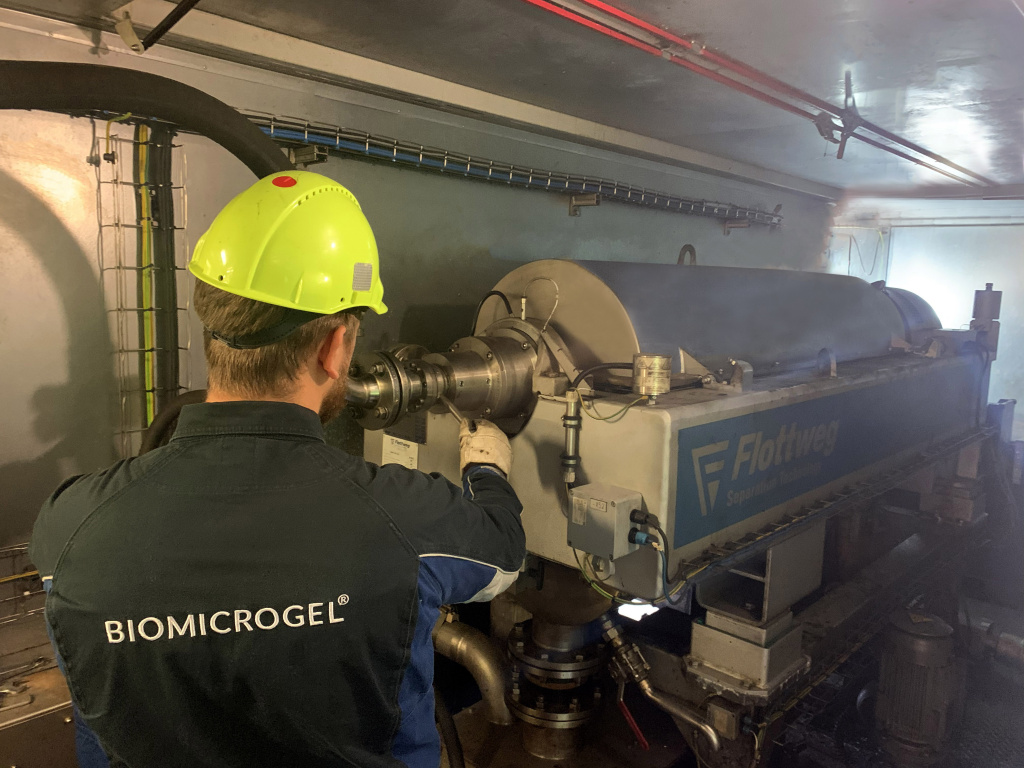
The customer has set the following requirements for purified water: efficient reduction in the residual concentration of oil products, up to a level of no more than 10 mg / dm3; the pH level should be in the range of 6.5-8.5. Another challenge was to minimize the sludge from the use of coagulants. The technology currently used at the plant in Cherepovets results in the sludge volume reaching 20% of the processed coolant.
The BMG-P2-02-03 reagent proposed by the experts of SPC BioMicroGel to solve these problems effectively traps any mineral and vegetable oils, as well as petroleum products contained in water. After separation of the water-oil mixture, the purified water can be returned back to the technological cycle and reused. BMG-P202-03 combines well with almost any coagulants based on inorganic salts of polyvalent metals that remove suspended particles from water. It is also important that this polysaccharide-based reagent is obtained by complex processing plant raw materials: sugar beet pulp, apple pomace, cellulose and its derivatives. The biodegradable coagulant is completely safe for the environment and at the same time it helps easily separate even the most persistent emulsions.
The separation of metalworking fluids using BMG-P2-02-03 involves consecutive treatment of a water-in-oil emulsion with mineral acid, a coagulant and an activator. The acid destabilizes the emulsion, releasing part of the oil products contained in it during the first stage. The use of a coagulant and an activator leads to the binding of oil products and the formation of a poorly soluble sediment, which is then separated by settling or filtration. At the final stage of purification, the pH-level of the clarified water is adjusted with a working solution of soda.
Pilot tests for the separation of spent metalworking fluids were carried out using the existing equipment of the oil-emulsion section of PJSC Severstal at natural temperature (22-27°C), without additional heating (the technology used at the enterprise requires heating the coolant to 85-95°C).
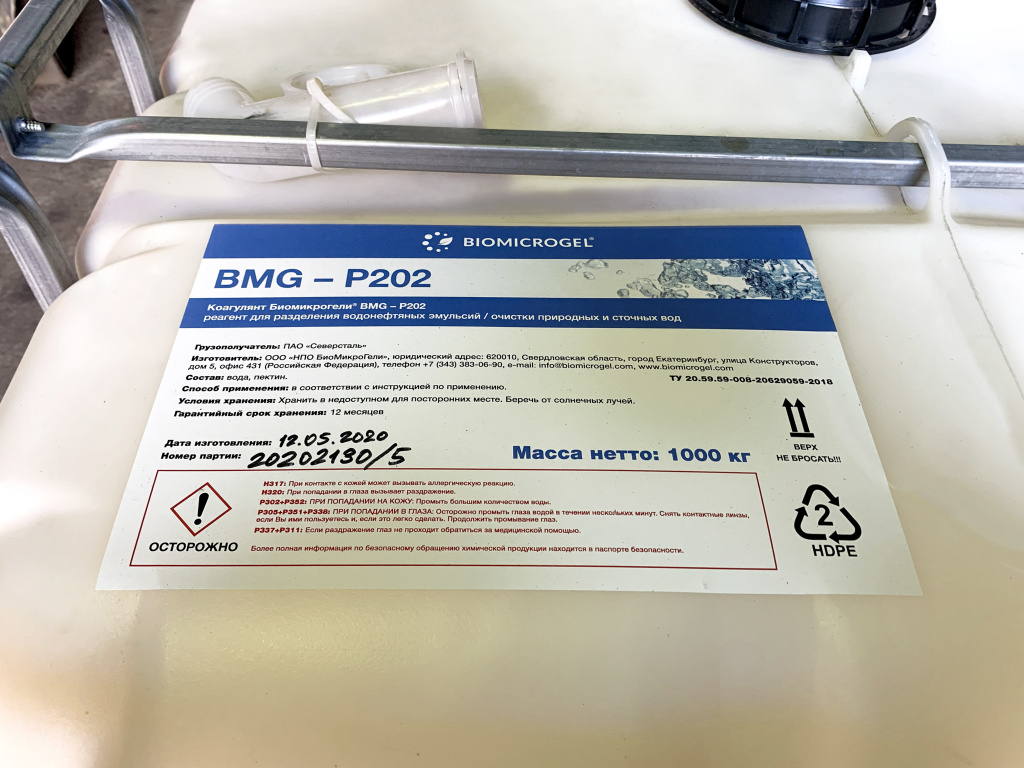
Biomicrogels® BMG-P2 coagulants can be supplied in the form of powder, solution or paste.
The tests lasted for 9 days, during which more than 1.5 thousand cubic meters of cutting fluid were processed. The average daily performance of the section during the pilot tests allowed to clean 300 m3 of fluid per day, which corresponds to the productivity of the existing technological chain.
As a result of experiments, the content of petroleum products in the water was less than 1 mg, which was mentioned in the letter of thanks to the general director of SPC BioMicroGel Andrey Elagin.
“The use of the coagulant from SPC BioMicroGel® made it possible to effectively separate the spent cutting fluid and achieve:
- reduction of the oil products content in water from 2500 mg / dm3 to <1 mg / dm3;
- pH value of purified water in the range of 6.5-8.0;
- no longer need to heat the metalworking fluid during the cleaning process;
- when a high-quality oil product is separated, there is a potential for reducing waste generation to zero” the letter says.
The tests in Cherepovets helped prove the possibility of separating cutting fluids with the highest possible concentration of oil products using the Biomicrogel® coagulants.
Our solution makes it possible to achieve the required residual content of oil products even when treating the most difficult industrial effluents, including, among others, spent metalworking coolants. I am convinced that the potential of these reagents will be appreciated not only at PJSC Severstal, but also at other leading enterprises of the pipe-rolling, metallurgical and engineering industries.
![]()
Andrey Elagin, Co-founder and CEO of BIOMICROGELS GROUP, General Director of SPC BioMicroGel.
![]()